Pattern Creation:
"FINAL CASTING QUALITY DEPENDS SOLELY ON THE WAX PATTERN
QUALITY."
- A wax model, also known as a pattern, is created in the shape of the desired part by injecting molten wax into a metal mold. Our wax pattern shop is equipped with both automatic and manual wax injection machines. We combine state-of-the-art machinery with skilled craftsmanship to achieve the highest possible quality of wax patterns.
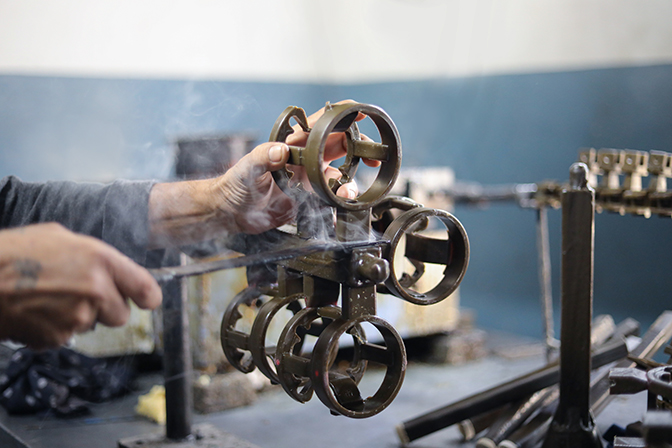
Pattern Assembly:
- Before assembly, each pattern undergoes a strict visual inspection. The wax patterns are then attached to a central wax sprue, forming a tree-like structure. This sprue acts as a channel for the molten metal to flow into the patterns during pouring.
Shell Building & drying:
- The wax assembly is dipped into a liquid ceramic slurry, coating the entire surface. Once the slurry dries, it is covered with fine ceramic sand using materials like zircon flour, fine sand, fused silica, and colloidal silica (water-based). This process is repeated several times with progressively coarser layers to build a strong and durable shell around the wax patterns.
- We have temperature and humidity controlled drying rooms equipped with dehumidifiers to achieve the desired moisture level before the dewaxing process.
Dewaxing:
- The ceramic shell is placed in a furnace to undergo autoclaving, where the wax melts and drains out, leaving a hollow cavity in the shape of the desired part. The wax can be collected and reused for future patterns. We utilize an industry-standard automatic dewaxing plant for this process
Shell Firing:
- The ceramic shell is fired at high temperatures to remove any remaining wax residue and harden the shell. This step also eliminates moisture and impurities, further strengthening the shell.
Melting & Pouring:
- Molten metal is poured into the preheated ceramic shell. The metal flows through the sprue and into the cavities left by the wax patterns, capturing all the intricate details of the part. Our melting shop is equipped with INDUCTOTHERM induction furnaces, featuring 150KV and 300KV crucibles.
Shell Removal:
- Once the metal has fully solidified, the ceramic shell is removed using vibratory equipment. Any remaining shell material is eliminated through sandblasting or other in-house cleaning processes.
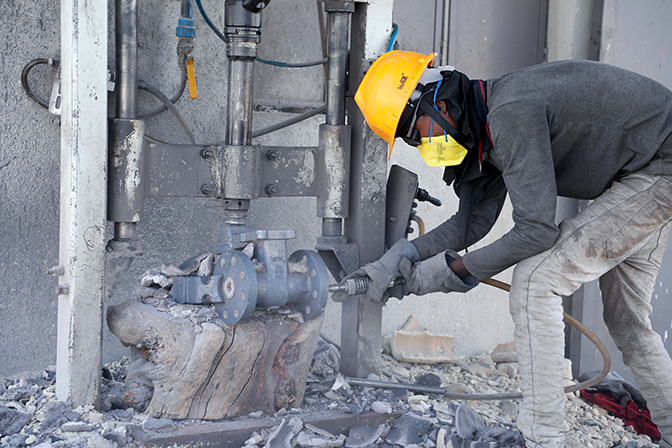
Gate Cutting & Grinding:
- The individual metal parts are cut from the sprue using gas-cutting or saw-cutting methods. Remaining sprue material and any imperfections are ground down to achieve the desired surface finish and dimensional accuracy.
Shot Blasting:
- Shot blasting is performed to clean the castings and prepare the surface for further finishing processes. This process removes any remaining scale, rust, or other surface contaminants, ensuring a smooth and clean surface for the final product.
Fettling and Finishing:
- Skilled hands ensure the removal of any remaining shell material and imperfections to achieve a clean, clear casting with the desired surface finish.
Heat Treatment:
- Our in-house facility offers heat treatments such as solution annealing, normalizing, and tempering using temperature-controlled gas-fired furnaces. We ensure the best heat treatment practices through the study of microstructures.
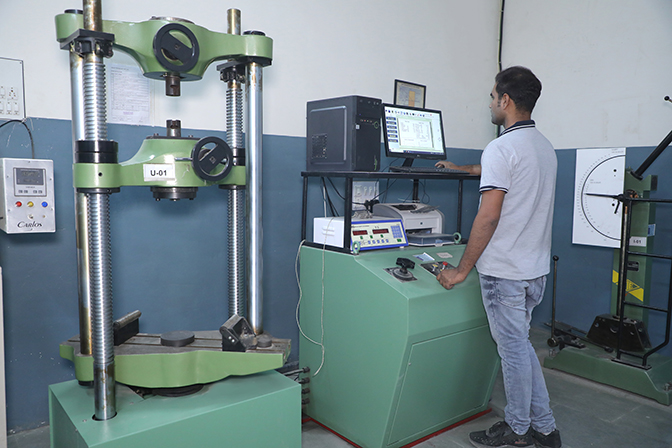
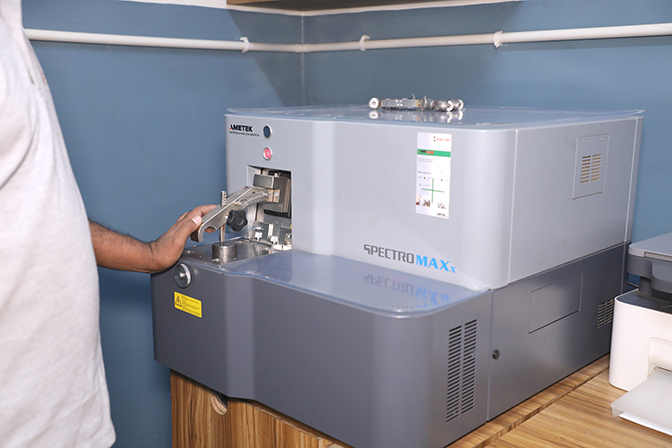
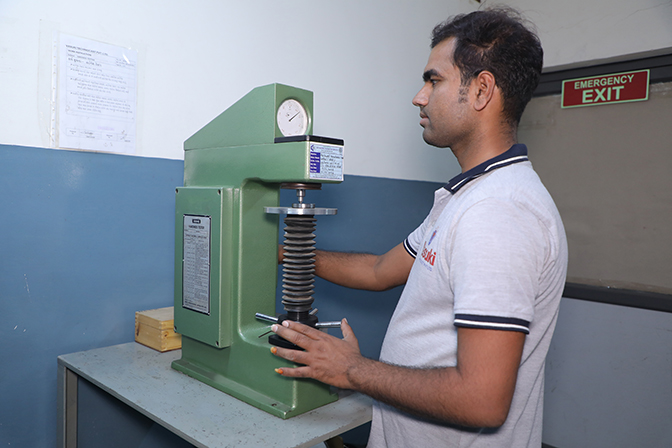
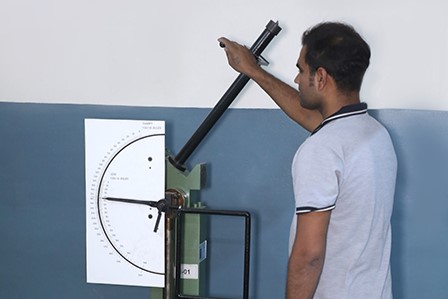
Finishing & Inspection:
- Each lot undergoes visual inspection for dimensional accuracy, surface finish, and material quality before packaging and dispatch.
Machining:
- We perform machining based on customer drawings and required accuracy. Our capabilities include VMC, CNC, and HMC machining.
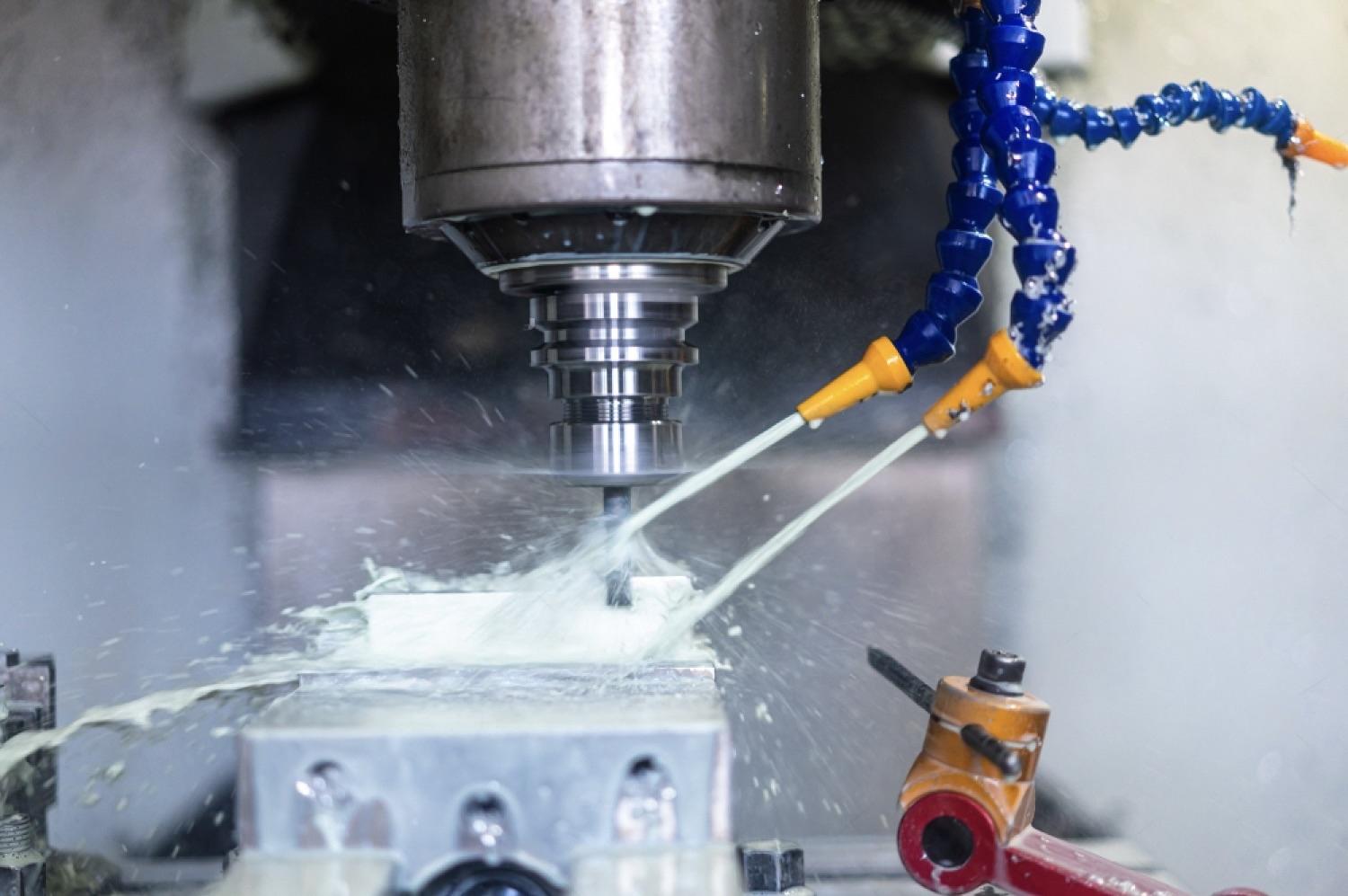